Monday, January 26, 2015
Keel Completed Chine Started
Really, the title is a bit of a misnomer as there was very little left to do on the keel and Ive only just started initial fitting of the chines. But it has been a while since I posted and the next round of work is going to be a lot of trial and error fitting with little to show, so rather than delay the next article, I am providing this short update.
All that remained to do on the keel was to add the hardware that fastens it to the frames, the stem, and the knee. The frames were fastened using #14 3 inch wood screws. The holes had to be recessed so that the screw heads are below the level of the keel. This is because eventually this surface will be faired at an angle to match the frame contours and I needed to insure that the screw heads would not be sticking up too high after the fairing.
I didnt have any good way of determining how deep to recess the heads other than to eyeball the angles of the frames and try and visualize where they would meet in the thickness of the keel. Then I recessed the holes slightly below where I though that angle was.
I learned a quick lesson in the application of these screws. All of these need to be pre-drilled and I did so, however, the drill bit was a bit on the small side. When I attempted to screw down the first screw, it got most of the way in and then snapped off!!
I had to break out a trusty screw extractor and after some effort, I managed to remove the broken off screw. I then went back though the hole with a slightly larger drill and was able to install all the remaining screws with no problem. One additional step I took was to place a small amount of epoxy resin in each screw hole before putting the screw in. This helps to seal the hole and the screw. After getting it into place I added an additional small amount over the screw head to completely seal it.
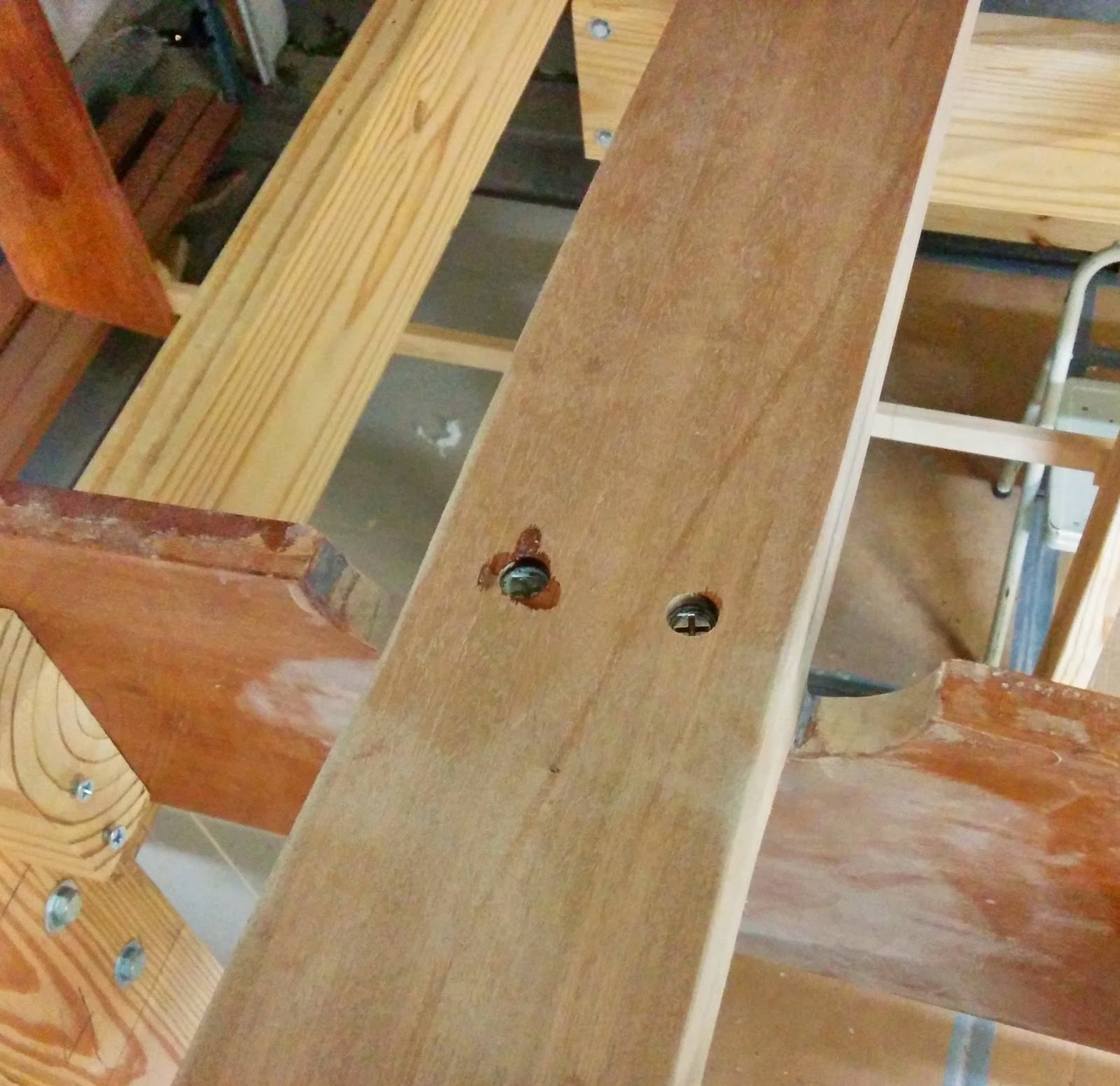
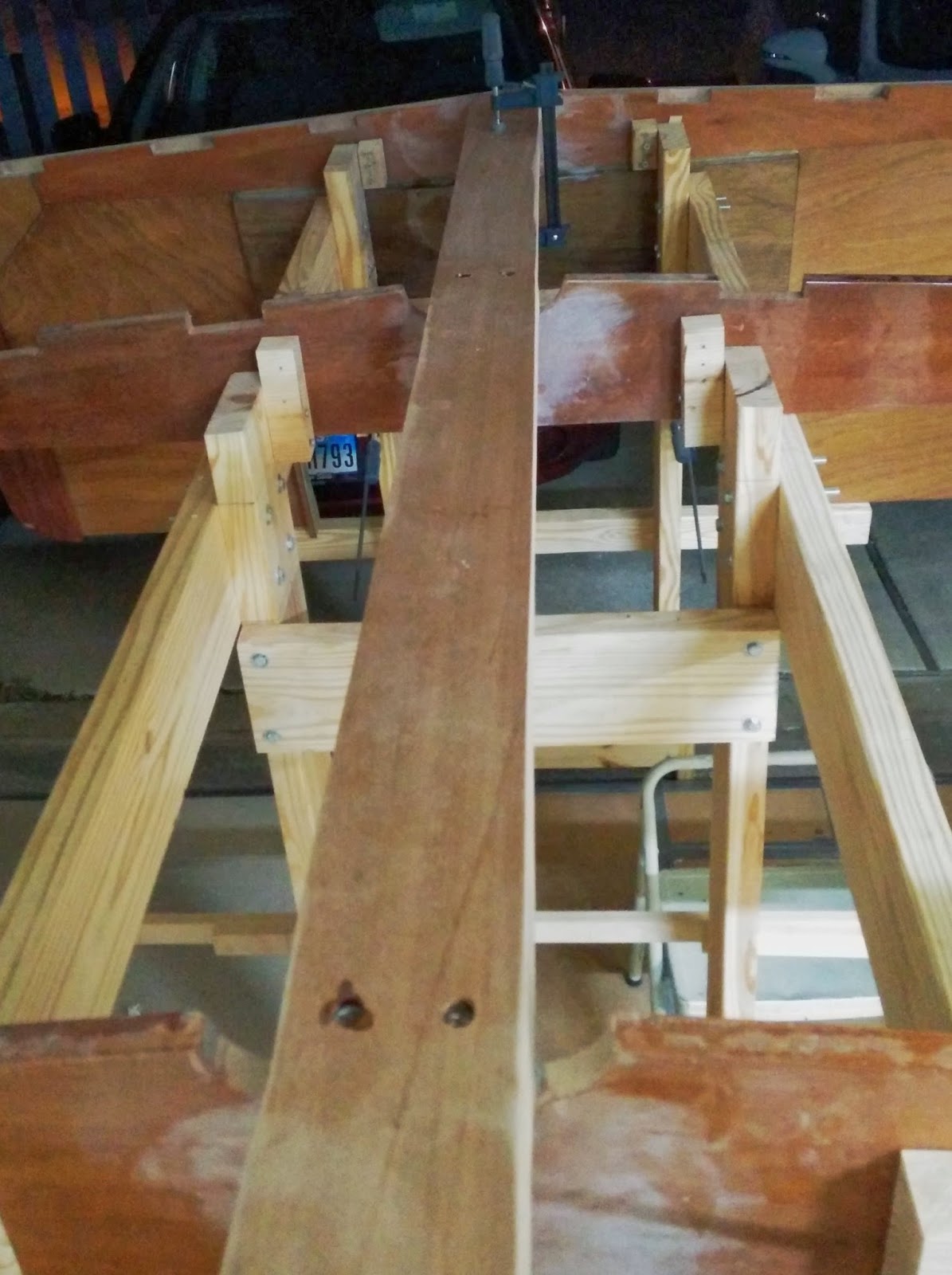
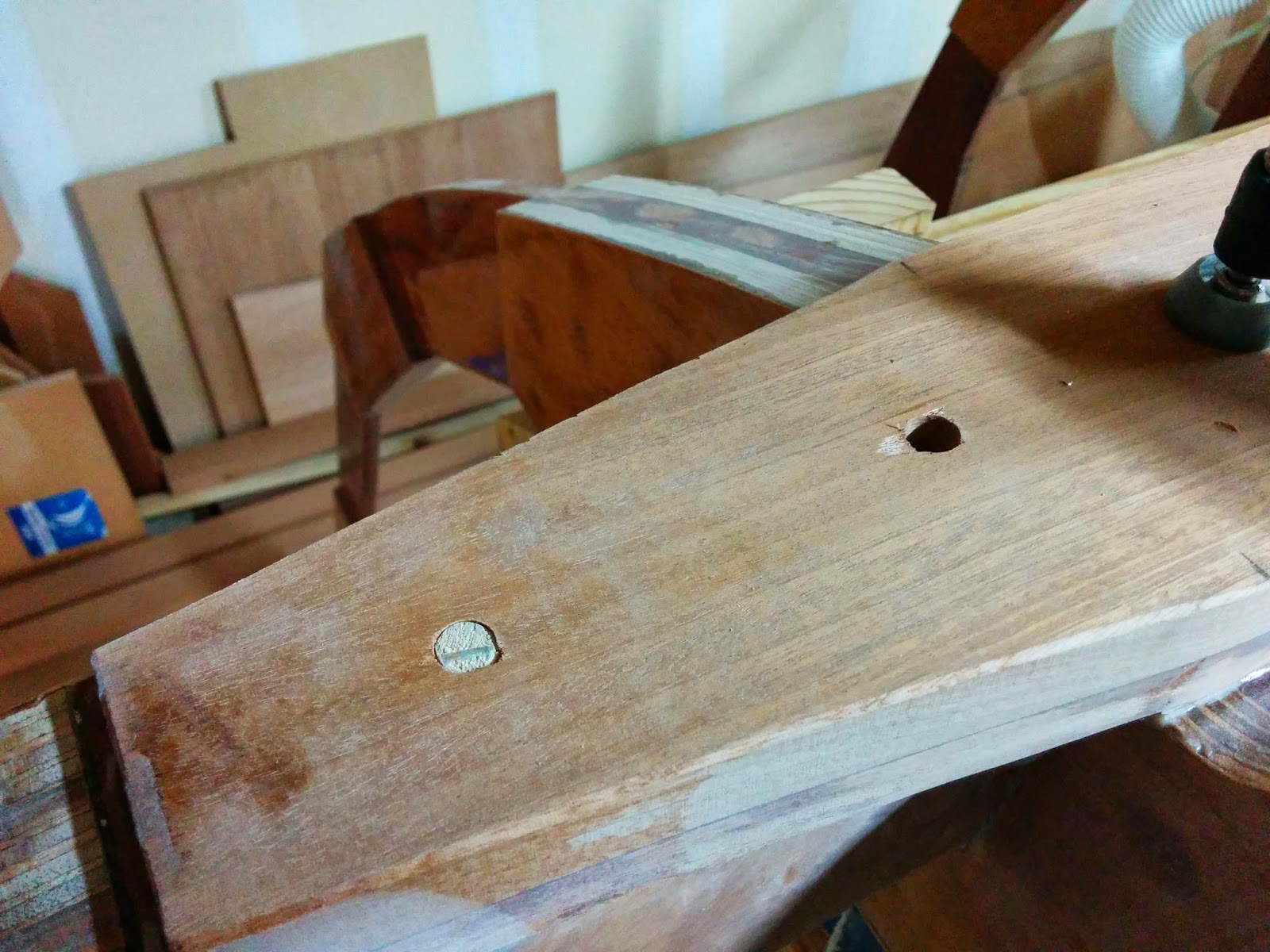
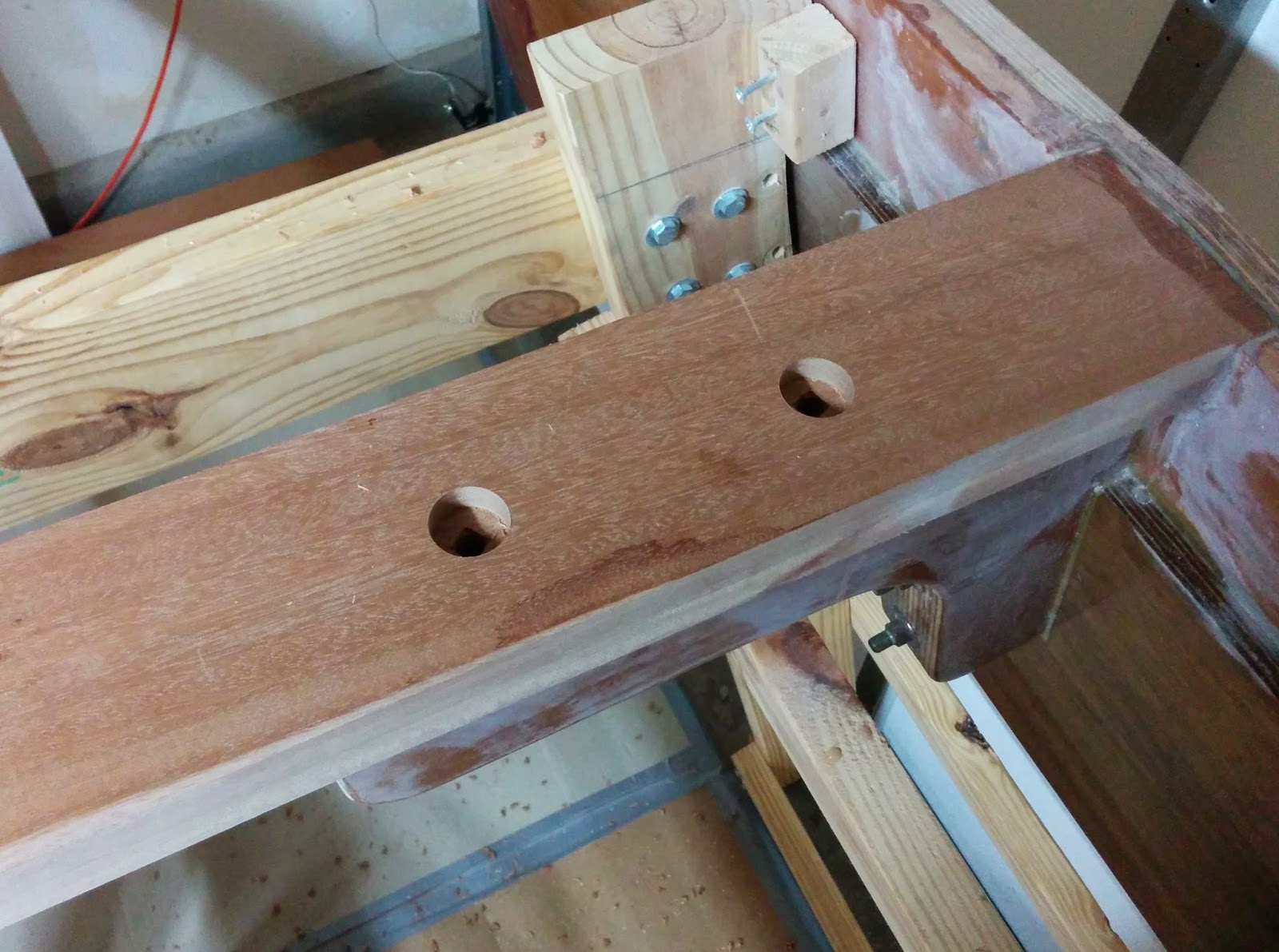
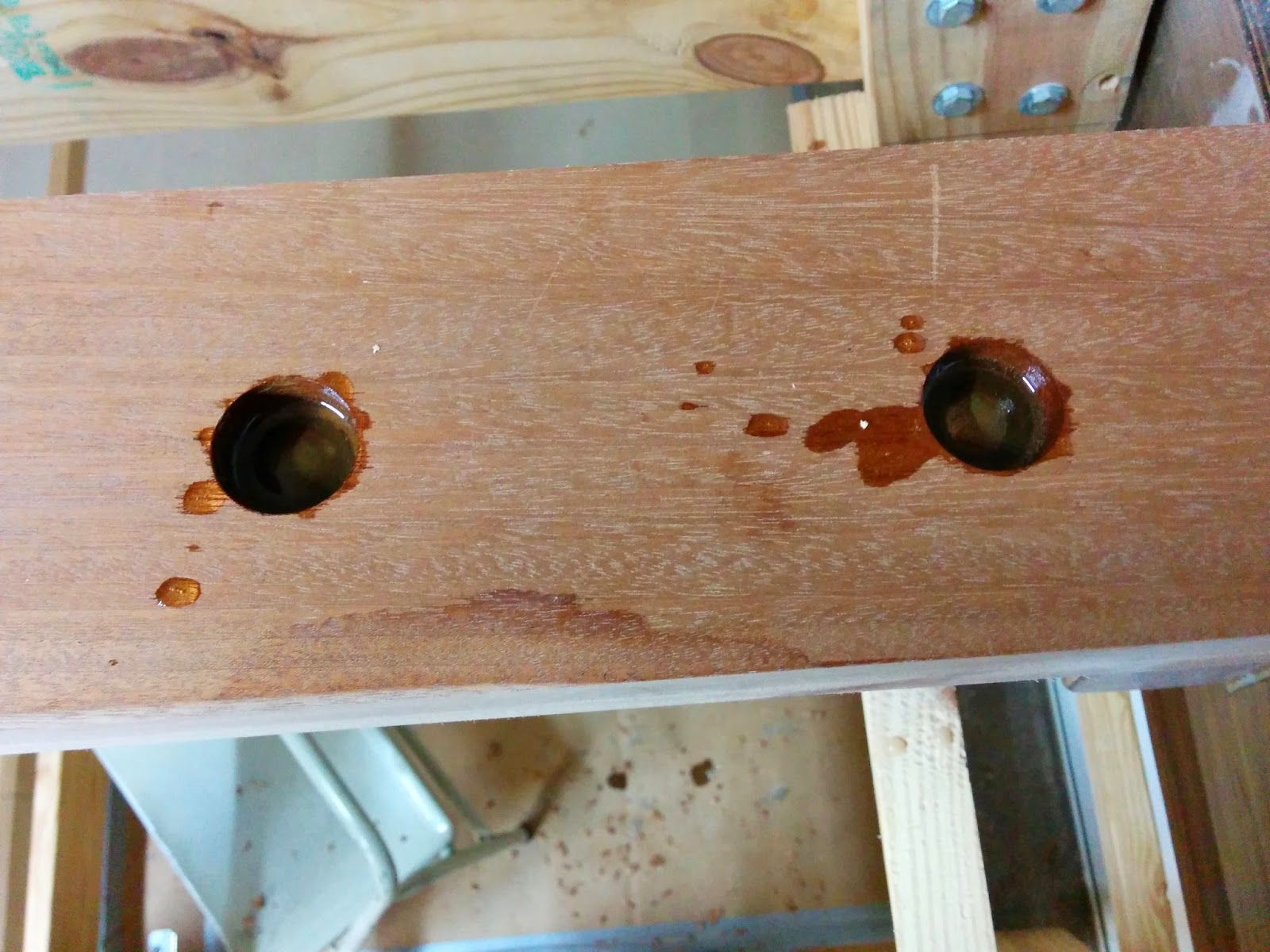

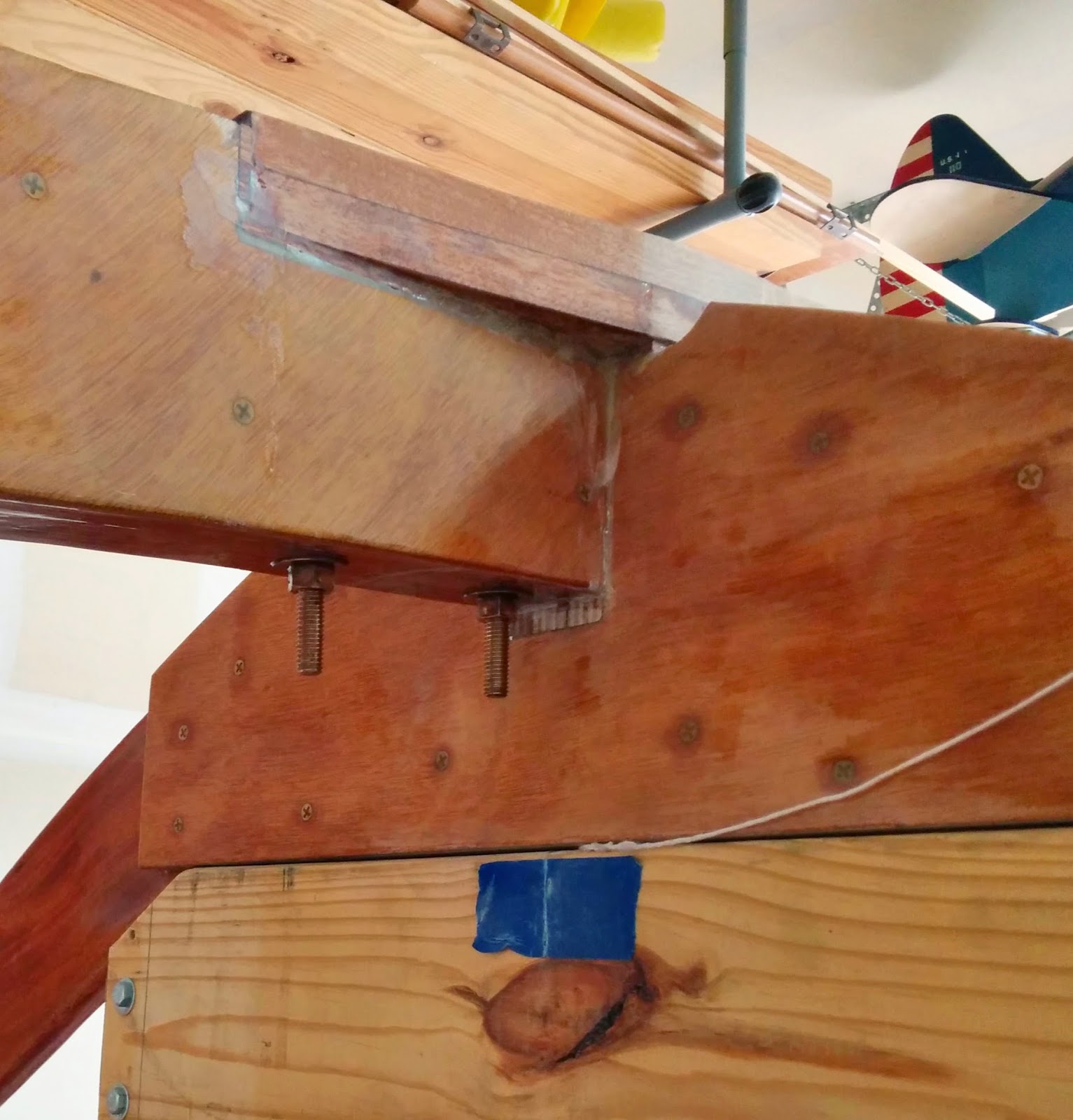
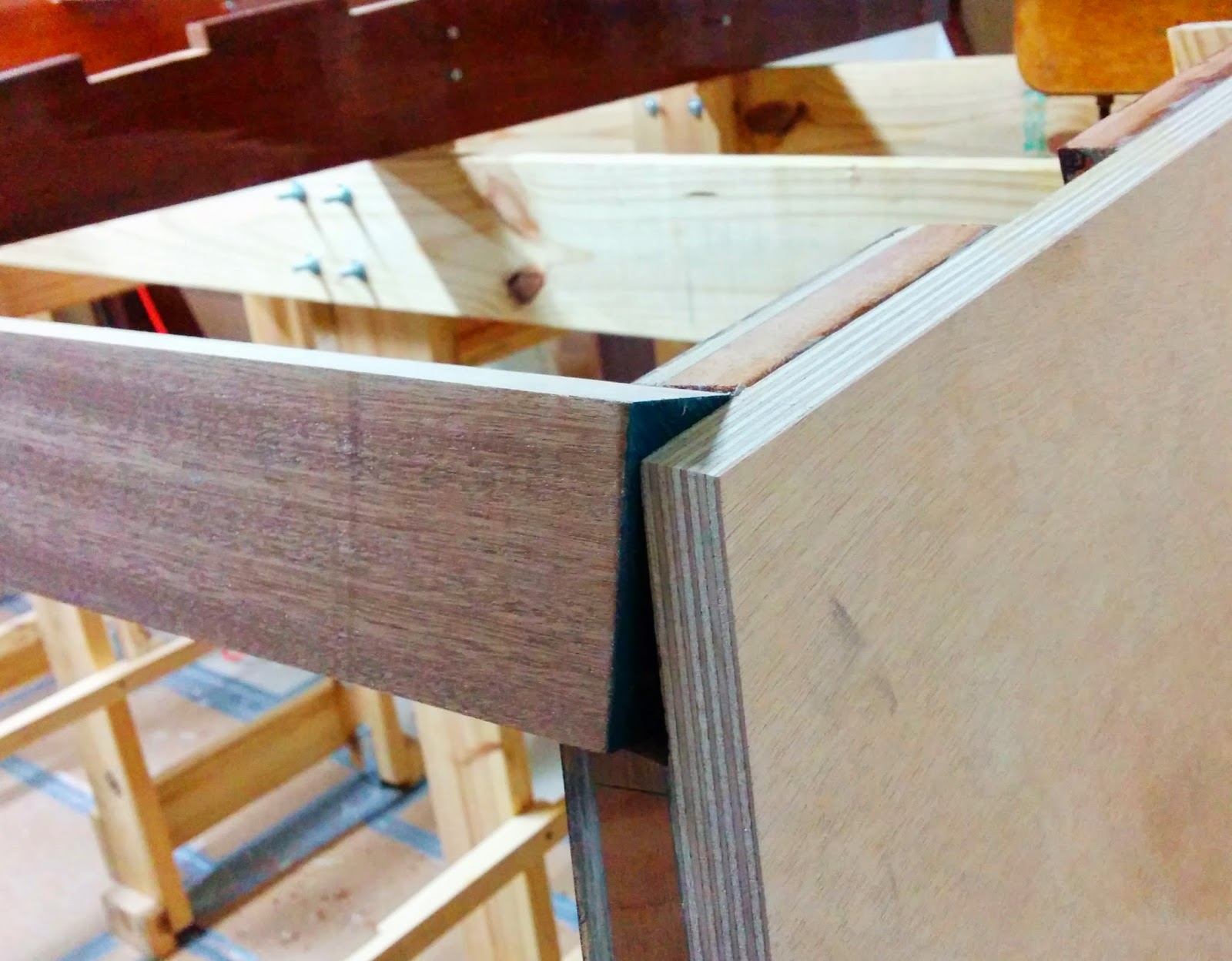
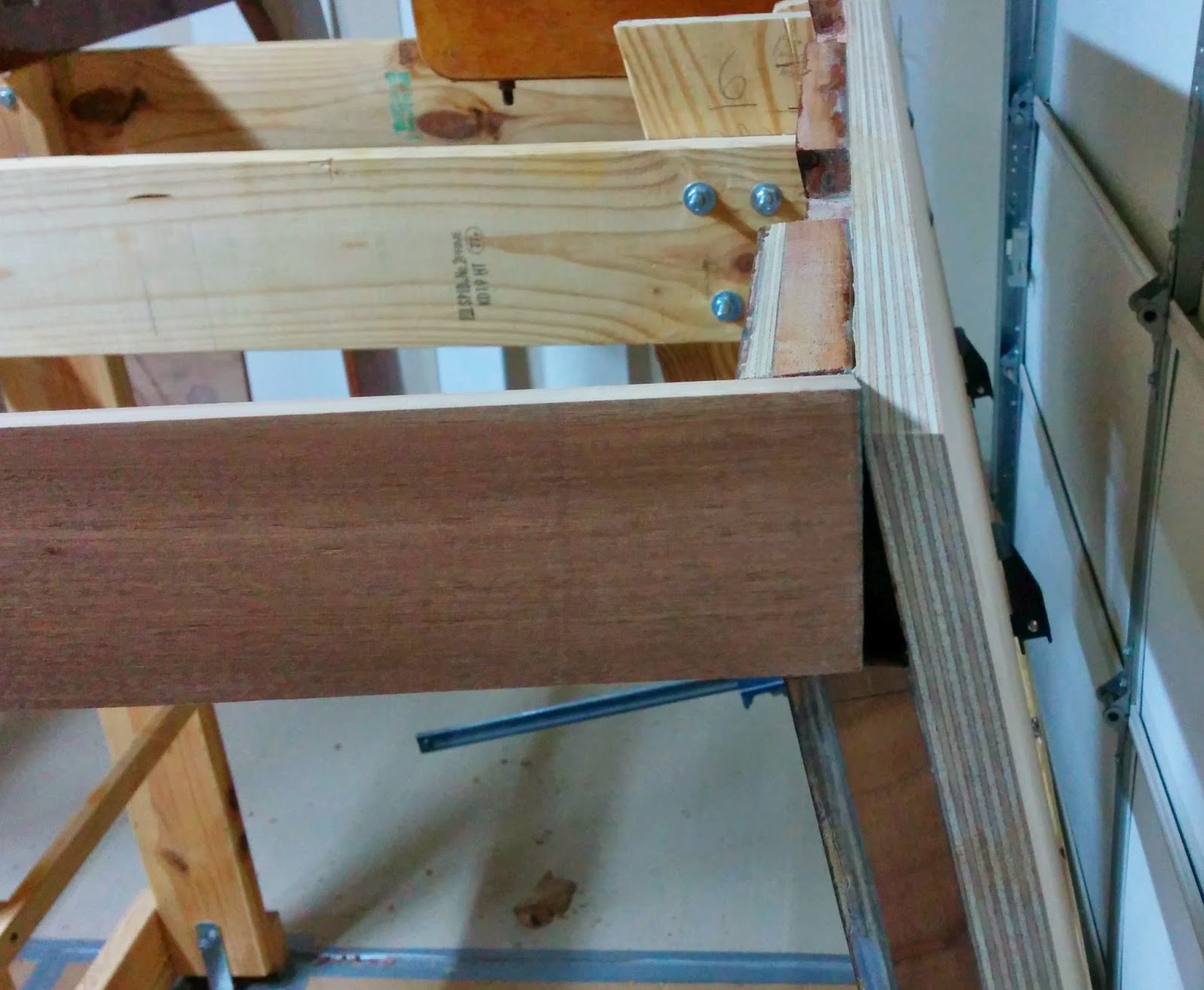
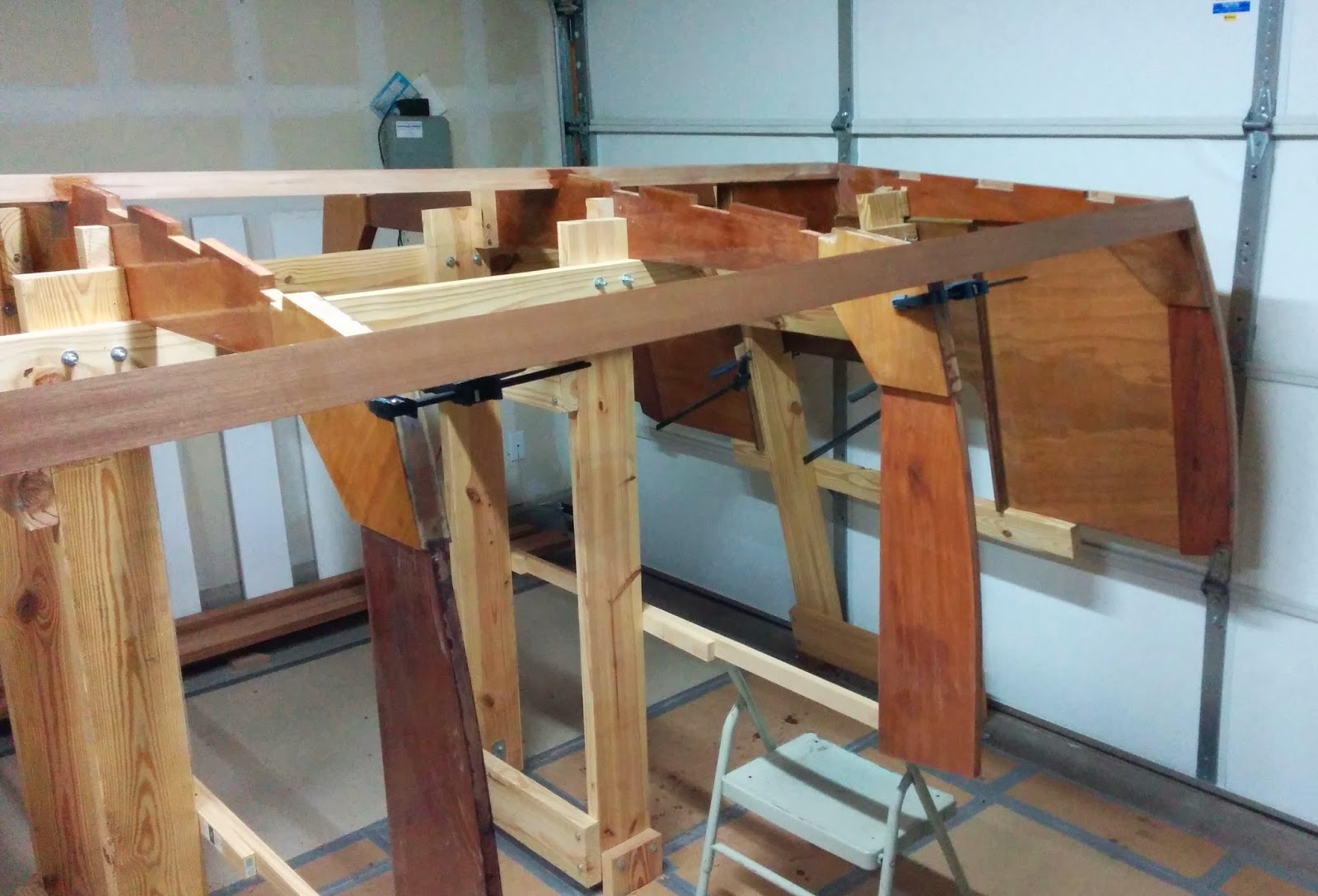
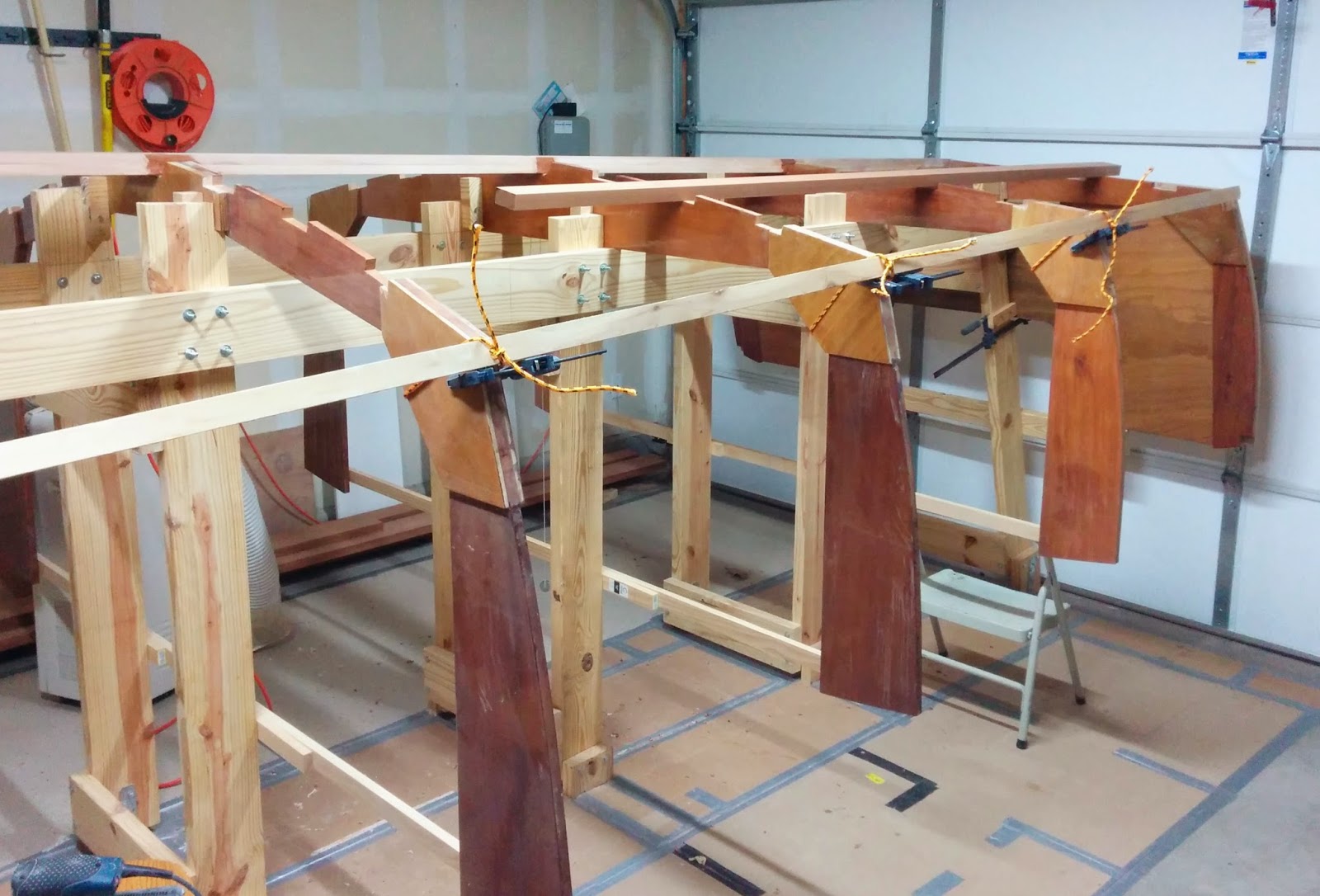
All that remained to do on the keel was to add the hardware that fastens it to the frames, the stem, and the knee. The frames were fastened using #14 3 inch wood screws. The holes had to be recessed so that the screw heads are below the level of the keel. This is because eventually this surface will be faired at an angle to match the frame contours and I needed to insure that the screw heads would not be sticking up too high after the fairing.
I didnt have any good way of determining how deep to recess the heads other than to eyeball the angles of the frames and try and visualize where they would meet in the thickness of the keel. Then I recessed the holes slightly below where I though that angle was.
I learned a quick lesson in the application of these screws. All of these need to be pre-drilled and I did so, however, the drill bit was a bit on the small side. When I attempted to screw down the first screw, it got most of the way in and then snapped off!!
I had to break out a trusty screw extractor and after some effort, I managed to remove the broken off screw. I then went back though the hole with a slightly larger drill and was able to install all the remaining screws with no problem. One additional step I took was to place a small amount of epoxy resin in each screw hole before putting the screw in. This helps to seal the hole and the screw. After getting it into place I added an additional small amount over the screw head to completely seal it.
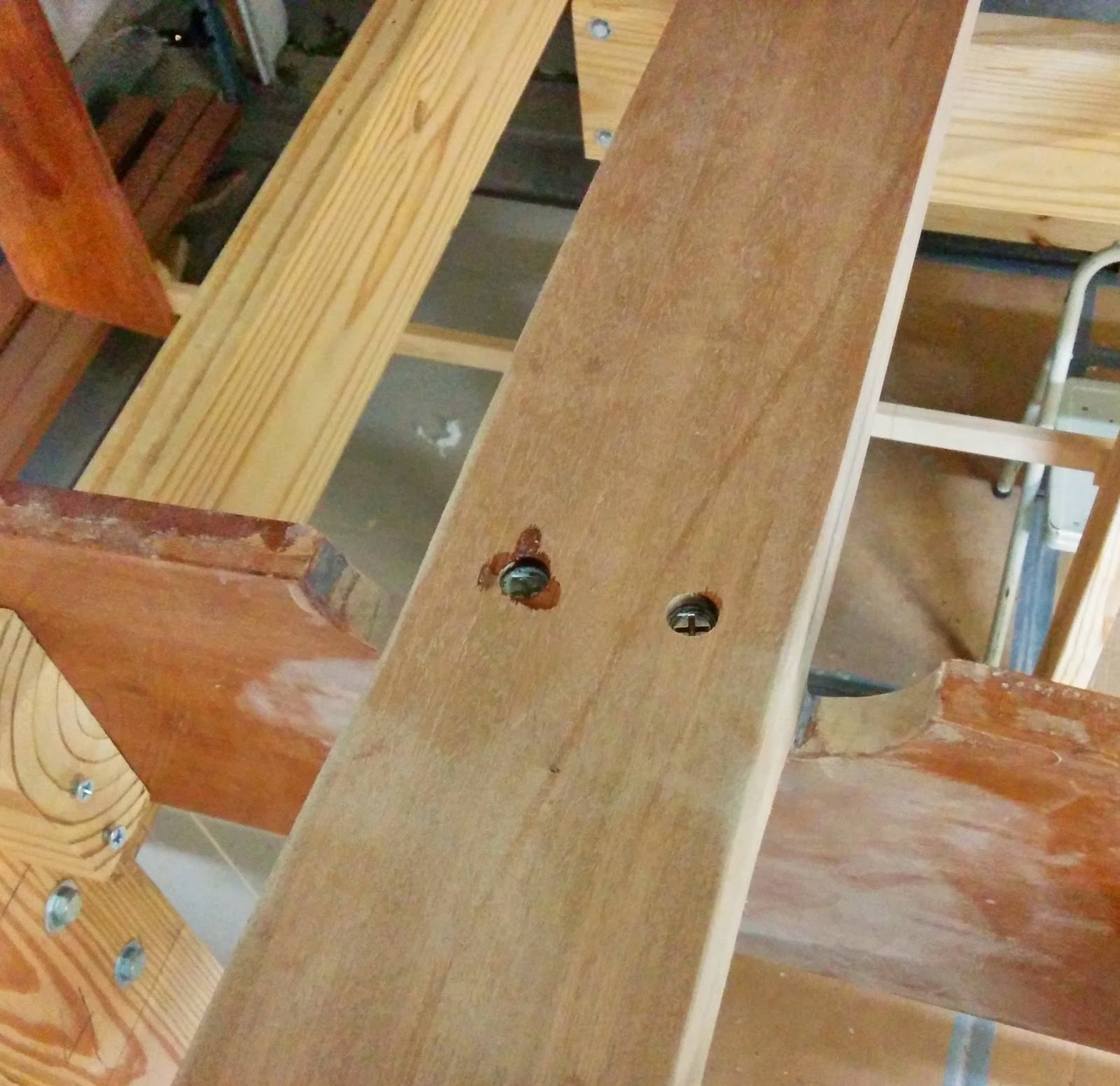
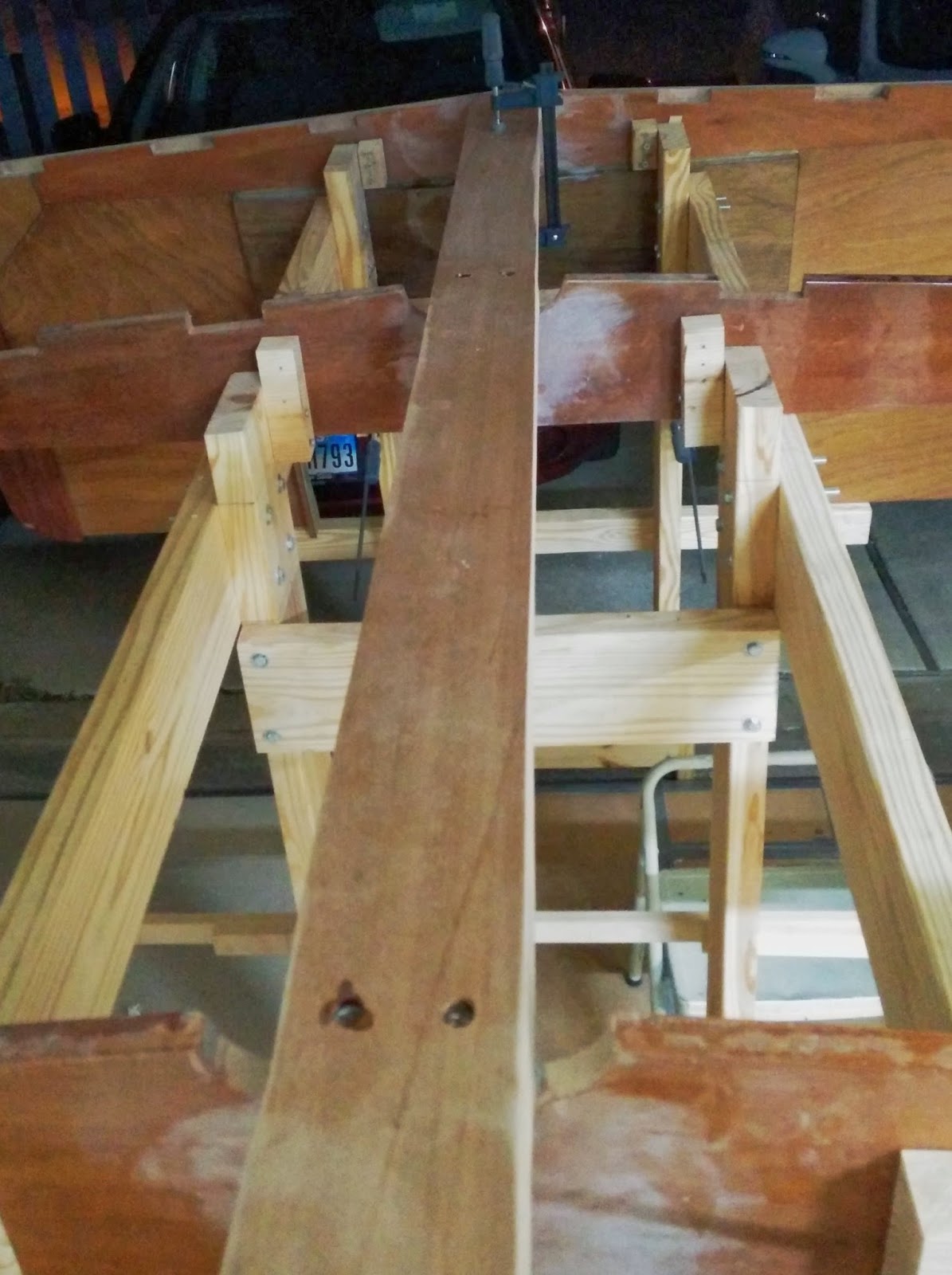
The stem and knee are fastened to the keel using the 6" long 3/8" carriage bolts and a matching washer and nut. I had previously drilled the holes in the stem and knee before attaching the keel and simply had to back drill through these holes to make the holes in the keel after it was installed.
Like the screw holes, the bolt heads also need to be recessed. The heads in the stem area are especially at risk of sticking up as quite a bit of keel will be faired away in this area. I bought a 1" Forstner bit to recess the hole. This simply cuts a 1" hole. I didnt want to drill all the way through, simply a small amount to provide the recess for the bolt heads.
The Forstner bit uses a centering point when drilling. This would normally cut into virgin wood as the larger hole is being cut. However I already had 3/8" holes in place. I needed some way to give the Forstner bit a centering point to bite into. What I did was temporarily insert 3/8" dowel rods into the holes before drilling. This worked great.
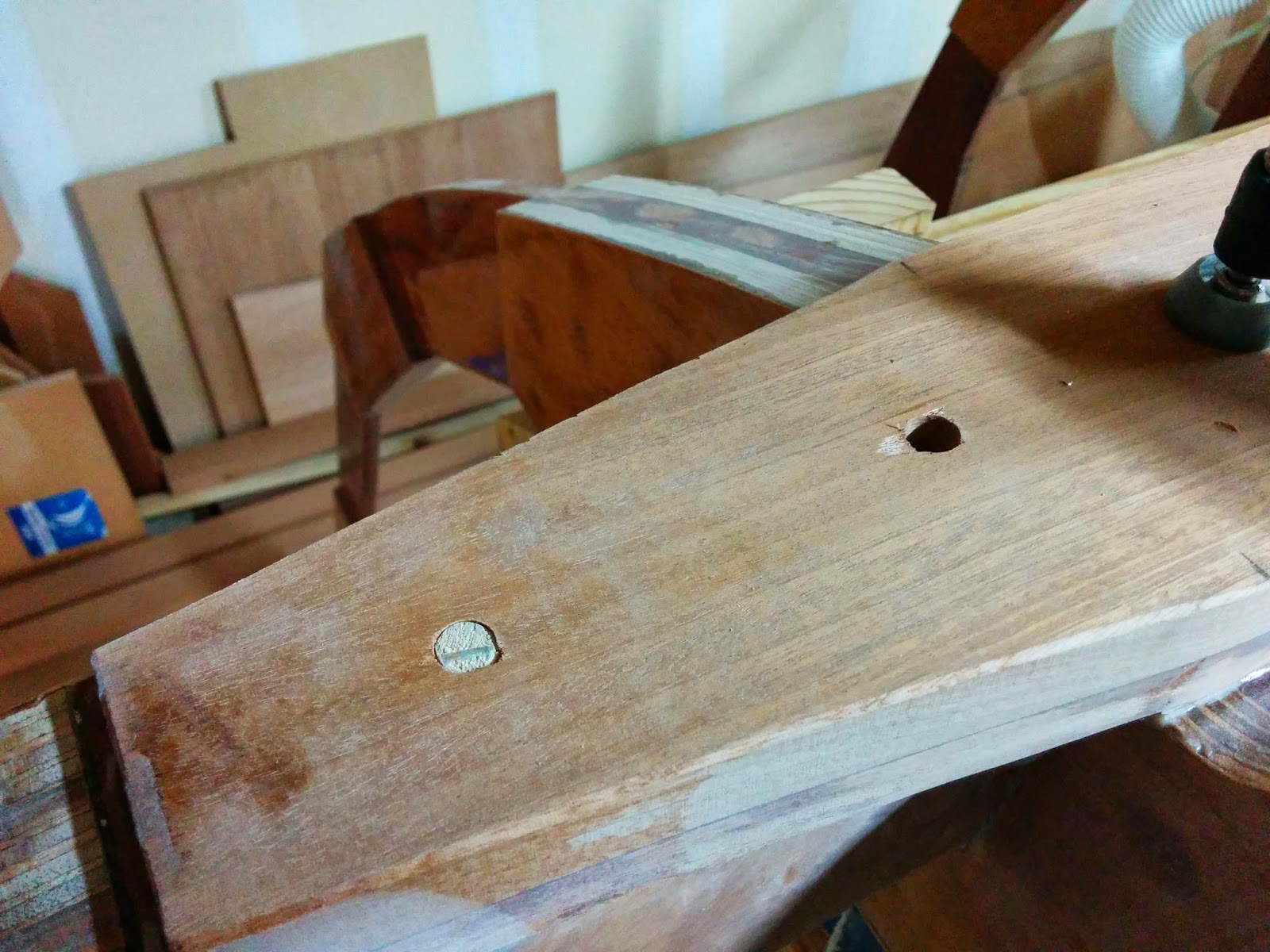
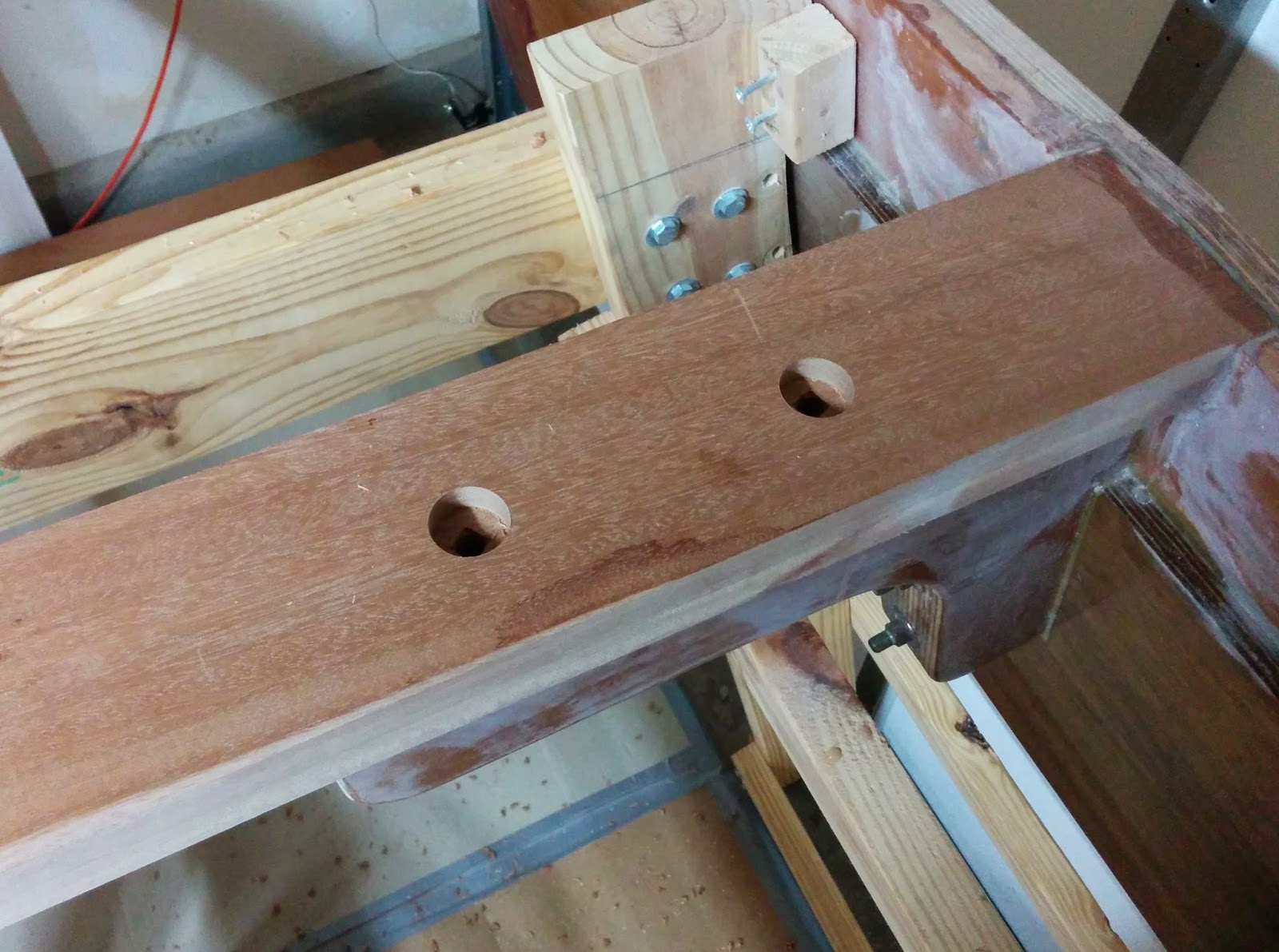
The knee bolts fit just fine and I quickly had them into position and tightened down. Like the screws, I applied epoxy resin on the bolt holes and around the bolt heads.
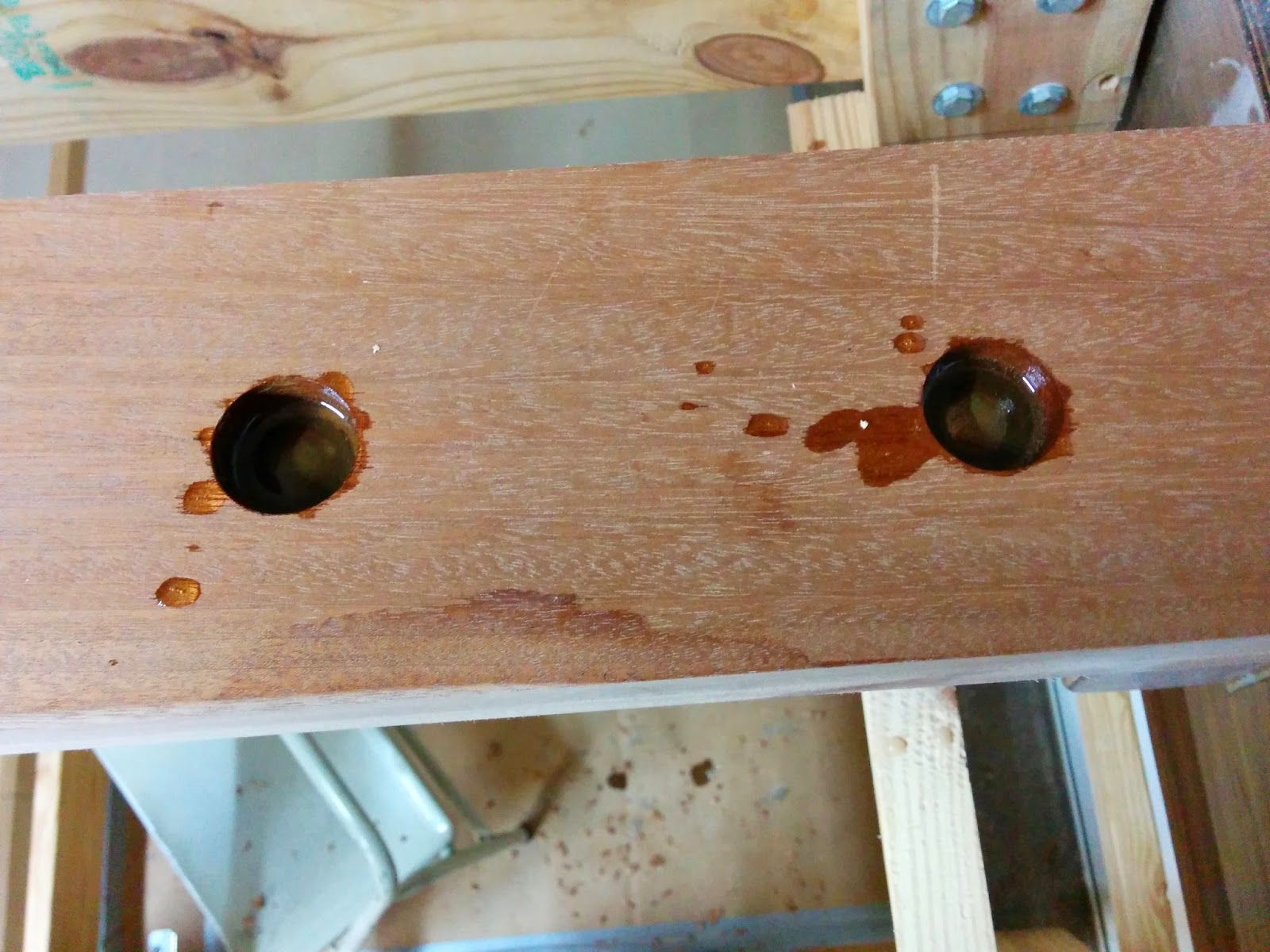

The stem bolts were a bit of a problem. Because of the notch in the stem and the recess for the bolt heads, the bolts were too long and when pressed all the way through the holes, I had smooth shank material showing in addition to the threaded portion of the shank. Ideally you want little or no smooth portion showing so that when the nut is tightened down, it doesnt hit the end of the threads before tightening up against the part.
The amount of smooth shank was too much to cover with washers. Good mechanical practice says that a maximum of two washers should be used with one washer being ideal. So I had to buy a tap and die set and add additional threads to the bolts. With smaller bolts this is not usually too hard, but these 3/8" bolts were fairly tough to add threads to. Fortunately they are bronze rather than stainless steel so the material is not as hard.
After these bolts were inserted and tightened down, they had excess threads showing past the nut. I simply sawed off the excess using a hacksaw and then cleaned up the ragged end with a file.
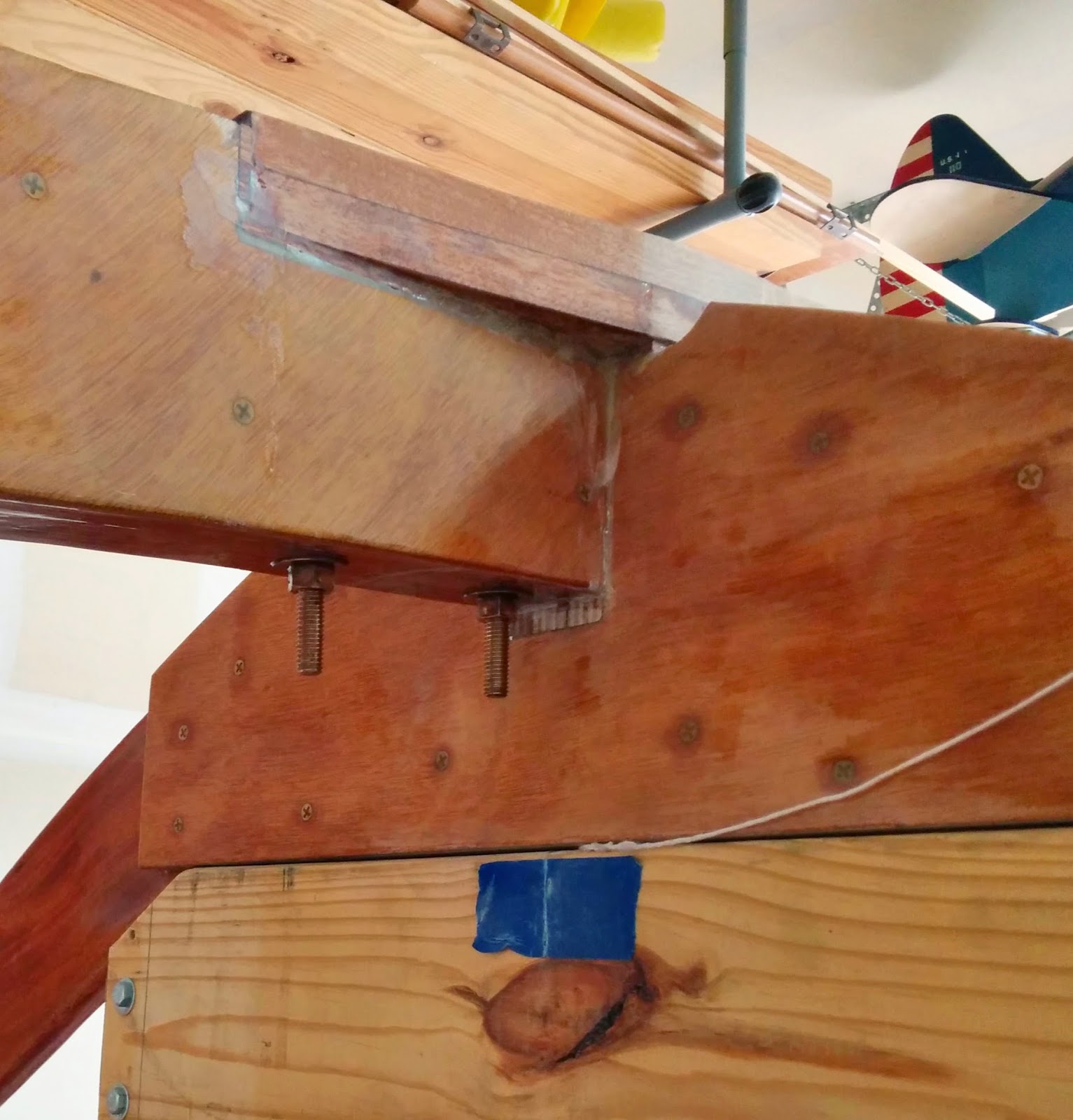
The final step in the process was to restore the encapsulation at various places on the frames, stem, and knee using fresh epoxy resin. This was accomplished and I could call the keel complete until I return to do the fairing.
Tonight, I started on fitting the chines. Readers will remember that these are the long horizontal members that connect the middle frame corners together in a similar fashion to the keel. This will be a fairly extensive process requiring cutting notches in the frames to accept the chine, making the chine members longer by scarf joining two pieces of lumber together, steaming and bending the chine to match the contour of the boat and fastening it into position. I will cover all of this as I get to it.
For today, I simply contented myself with seeing how the chine would fit and making the initial lines for the first frame notch cut. These notches are not simple straight cuts into the frames, but rather are cut at various angles to match how the chine meets up the frame. So each notch will have to be fitted, cut, fitted some more and cut again (if necessary) until the correct fit is established.
It is important to install the chine so there is excess material to fair away afterwards. This has to be taken into account when making the frame notches. The next photo shows approximately what this might look like. You can see that the side and top edges of the chine will eventually be faired away to match the shape of the boat so that the plywood skins lie flat against all pieces.
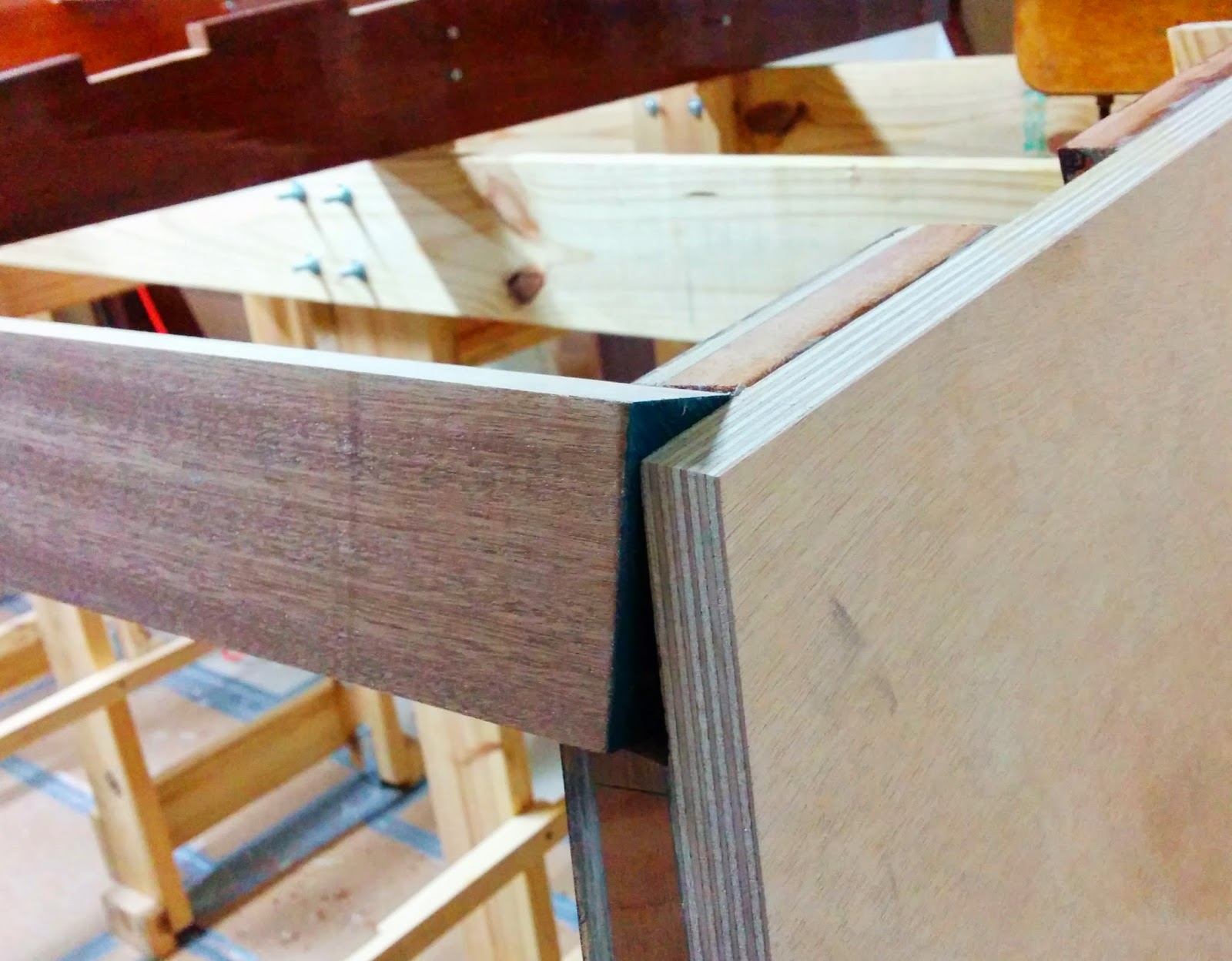
As mentioned previously, there are several angles to consider for each notch. The next photo illustrates an example of this. The chine will have to be cut so that it mates up to all the various angles or alternatively, the frame notches will have to be cut so that they mate up properly to the chine. Fun!!
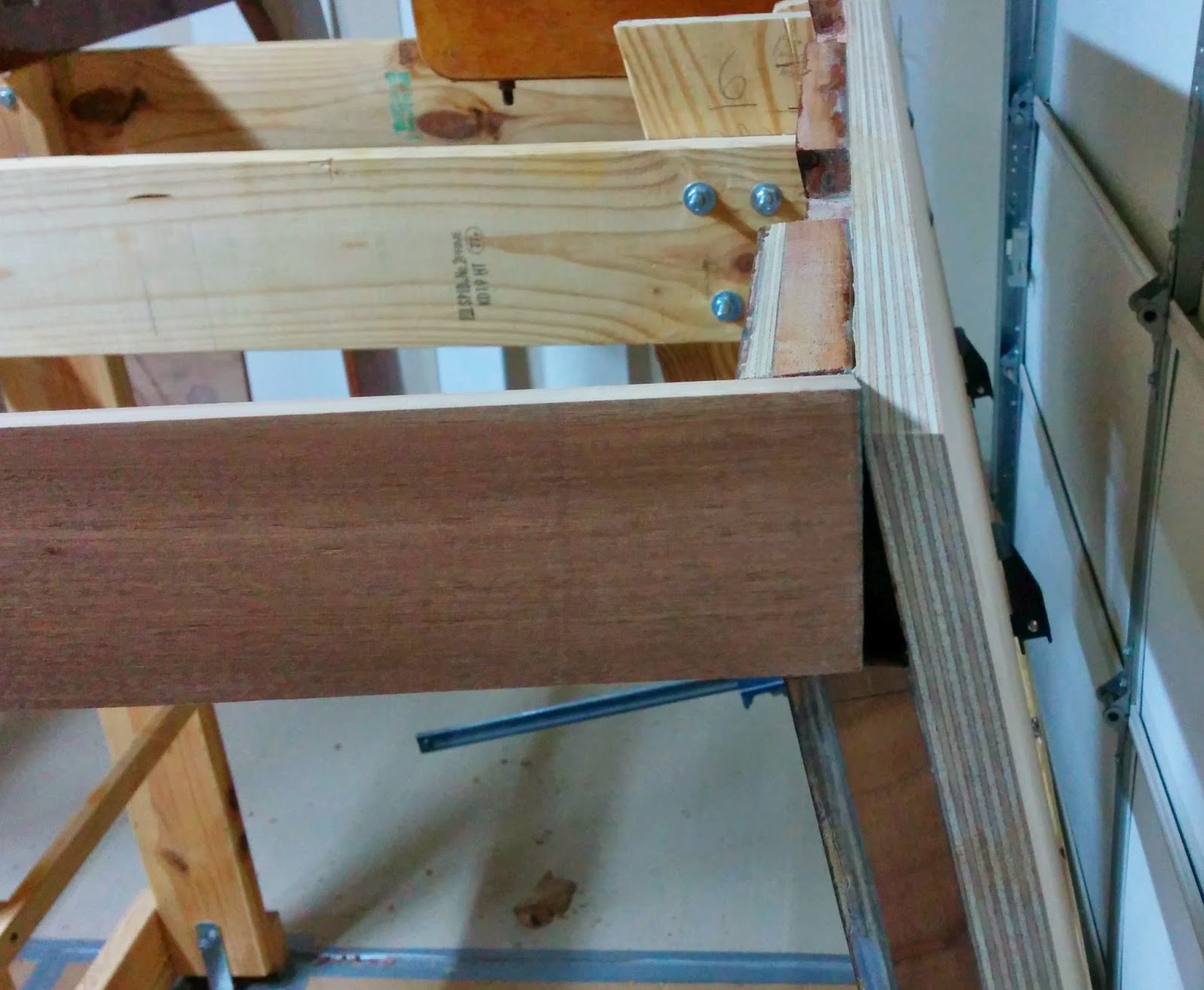
Im using a variety of long pieces of lumber including the chine lumber (the larger piece in the following photos) and the cedar batten I purchased last year. Mainly at this point, I am making sure that the chine wont have to be bent downwards to meet up to each frame corner. Bending inwards is fine and expected, but bending down would be a problem meaning that the frame was in the wrong position vertically.
This is where all that effort fitting the frames last year comes into play.The cedar batten confirmed that the frames are correctly placed.
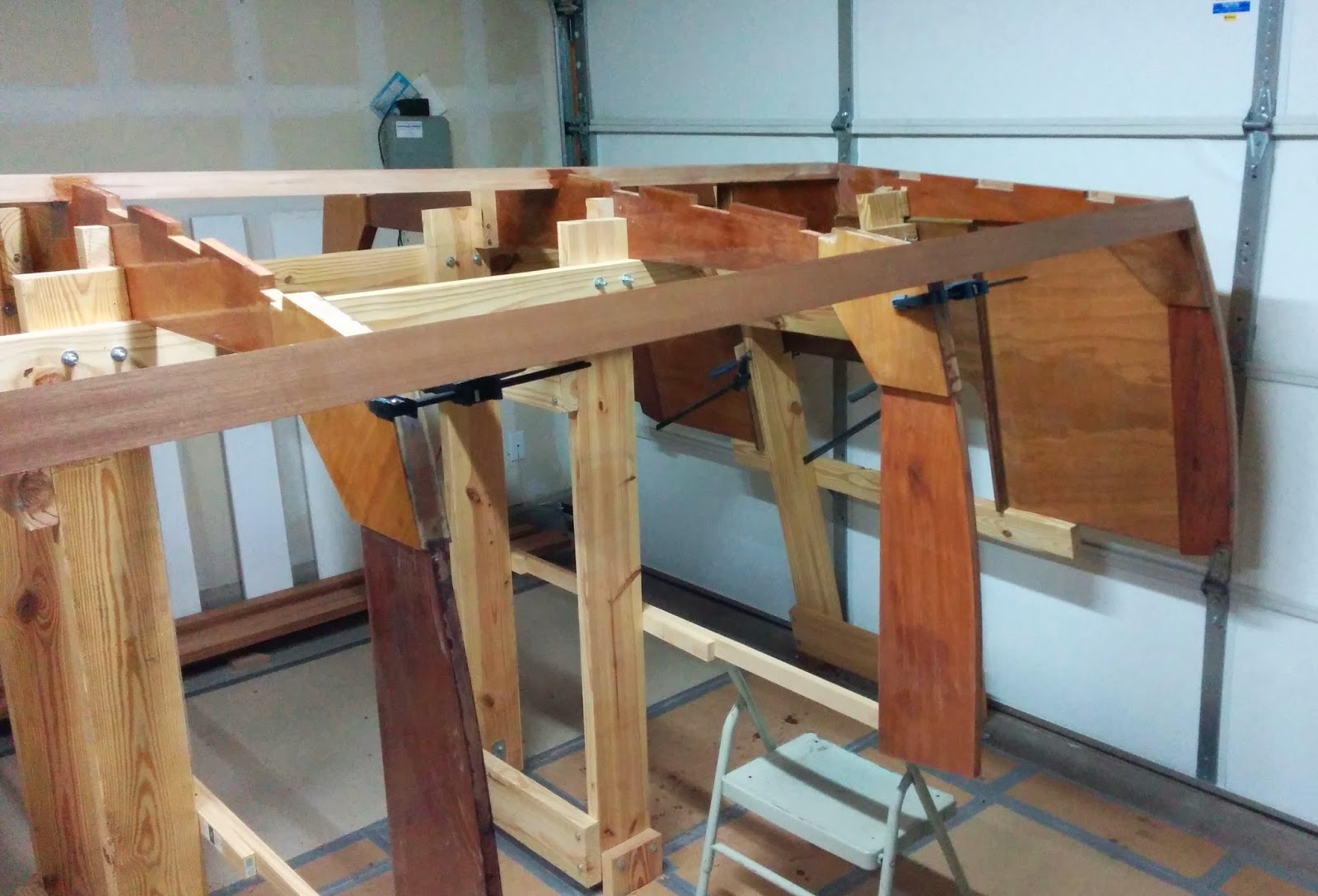
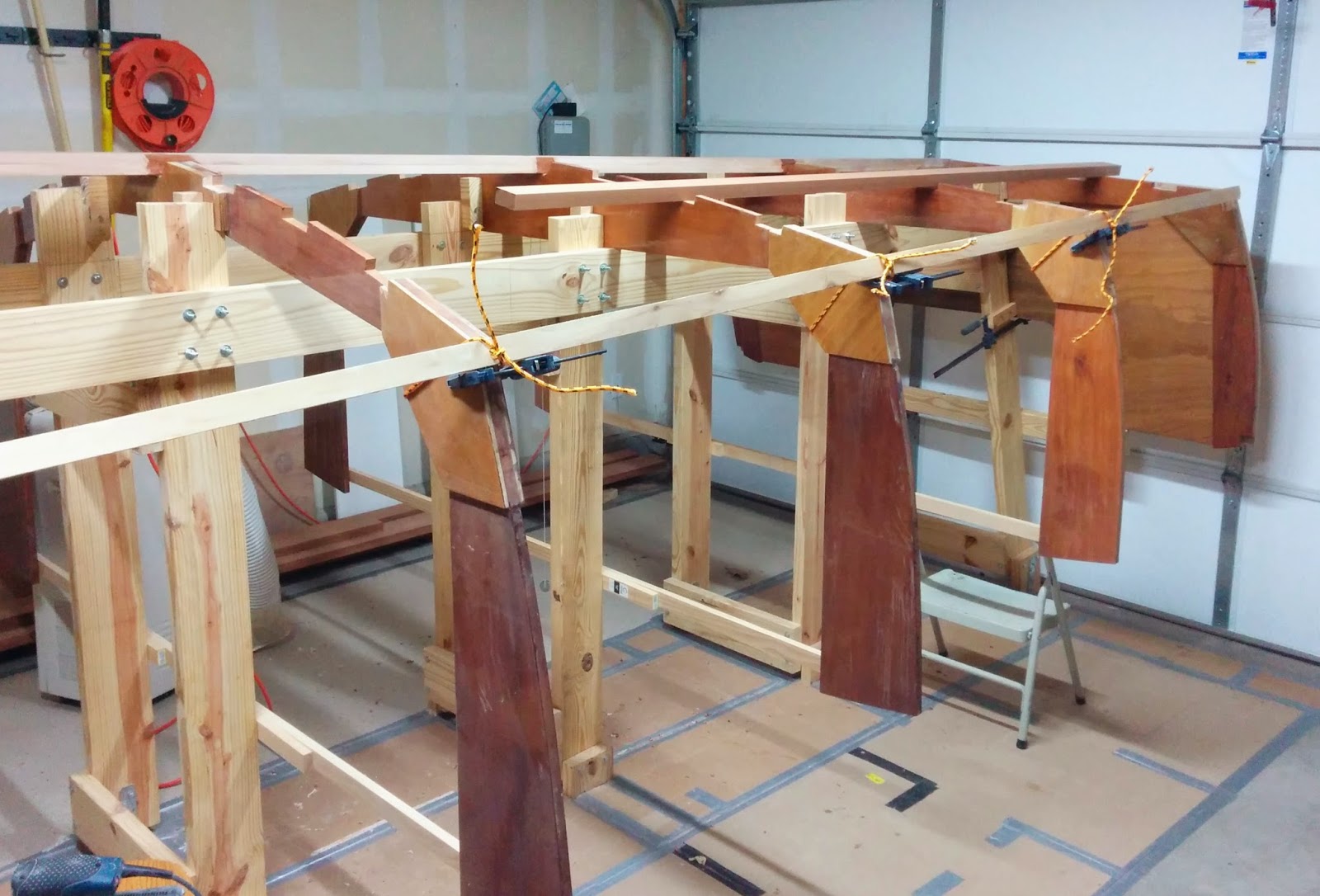
So that is it for the moment. I mentioned this process is going to be lengthy with little to show for the effort. But I will try to find interesting sections to include in the next posting. Until next time, take care.
Subscribe to:
Post Comments (Atom)
No comments:
Post a Comment